Abstract
Milling chatter is one of the biggest obstacles to achieve high performance machining operations of thin-walled workpiece in industry field. In the milling process, the time-varying and position-dependent characteristics of thin-walled components are evident. So, effective identification of modal parameters and chatter monitoring are crucial. Although the advantage of chatter monitoring by sound signals is obvious, the milling sound signals are nonstationary signals which contain more stability information both in time domain and frequency domain, and the common analytical transformation methods are no longer applicable. In this paper, short time Fourier transform (STFT) is taken as an example to compare the processing results with cmor continuous wavelet transform (CMWT). This article concerns the chatter detection and stability region acquisition in thin-walled workpiece milling based on CMWT. CMWT combines the advantages of the cmor wavelet and continuous wavelet transform which has good locality and the optimal time-frequency resolution. Therefore, CMWT can be adaptively adjusted signal by the window, which is very suitable for processing nonstationary milling signals. Firstly, the model and characteristics of thin-walled workpiece during the cutting process are presented. Secondly, the CMWT method for chatter detection based on acoustic signals in thin-walled component milling process is presented. And the chatter detection results and stability region acquisitions are analyzed and discussed through a specific thin-walled part milling process. Finally, the accuracy of the method presented is verified through the traditional stability lobe diagram predicted using the exiting numerical method and the machined surface morphologies at different cutting positions obtained through the confocal laser microscope.
Similar content being viewed by others
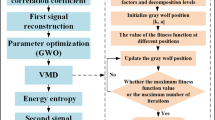
References
Song QH, Ai X, Tang WX (2011) Prediction of simultaneous dynamic stability limit of time-variable parameters system in thin-walled workpiece high-speed milling processes. Int J Adv Manuf Technol 55(9–12):883–889
Luo M, Luo H, Zhang D, Tang K (2018) Improving tool life in multi-axis milling of Ni-based superalloy with ball-end cutter based on the active cutting edge shift strategy. J Mater Process Tech 252:105–115
Ryabov O, Mori K, Kasashima N (1998) Laser displacement meter application for milling diagnostics. Opt Lasers Eng 30(3–4):251–263
Devillez A, Dudzinski D (2007) Tool vibration detection with eddy current sensors in machining process and computation of stability lobes using fuzzy classifiers. Mech Syst Signal Process 21(1):441–456
Pérez-Canales D, Vela-Martínez L, Carlos Jáuregui-Correa J, Alvarez-Ramirez J (2012) Analysis of the entropy randomness index for machining chatter detection. Int J Mach Tools Manuf 62(1):39–45
Lamraoui M, Thomas M, El Badaoui M (2014) Cyclostationarity approach for monitoring chatter and tool wear in high speed milling. Mech Syst Signal Process 44(1–2):177–198
Shao Y, Deng X, Yuan Y, Mechefske CK, Chen Z (2014) Characteristic recognition of chatter mark vibration in a rolling mill based on the non-dimensional parameters of the vibration signal. J Mech Sci Technol 28(6):2075–2080
Cao HR, Zhou K, Chen XF (2015) Chatter identification in end milling process based on EEMD and nonlinear dimensionless indicators. Int J Mach Tools Manuf 92:52–59
Gabriel RF, Alexandru E, Ionuţ CC (2012) Method for early detection of the regenerative instability in turning. Int J Adv Manuf Technol 58(1–4):29–43
Huang P, Li J, Sun J, Zhou J (2013) Vibration analysis in milling titanium alloy based on signal processing of cutting force. Int J Adv Manuf Technol 64(5–8):613–621
Luo M, Luo H, Axinte D, Liu DS, Mei JW, Liao ZR (2018) A wireless instrumented milling cutter system with embedded PVDF sensors. Mech Syst Signal Process 110:556–568
Tangjitsitcharoen S, Saksri T, Ratanakuakangwan S (2015) Advance in chatter detection in ball end milling process by utilizing wavelet transform. J Intell Manuf 26(3):1–15
Liu Y, Wu B, Ma J, Zhang D (2016) Chatter identification of the milling process considering dynamics of the thin-walled workpiece. Int J Adv Manuf Technol 2016:1–9
Tsai NC, Chen DC, Lee RM (2010) Chatter prevention for milling process by acoustic signal feedback. Int J Adv Manuf Technol 47(9–12):1013–1021
Nair U, Krishna BM, Namboothiri VNN, Nampoori VPN (2010) Permutation entropy based real-time chatter detection using audio signal in turning process. Int J Adv Manuf Technol 46(1–4):61–68
Hynynen KM, Ratava J, Lindh T, Rikkonen M, Ryynänen V, Lohtander M, Varis J (2014) Chatter detection in turning processes using coherence of acceleration and audio signals. J Manuf Sci Eng 136(4):044503
Thaler T, Potočnik P, Bric I, Govekar E (2014) Chatter detection in band sawing based on discriminant analysis of sound features. Appl Acoust 77(77):114–121
Marinescu I, Axinte DA (2008) A critical analysis of effectiveness of acoustic emission signals to detect tool and workpiece malfunctions in milling operations. Int J Mach Tools Manuf 48(10):1148–1160
Delio T, Tlusty J, Smith S (2008) Use of audio signals for chatter detection and control. J Manuf Sci Eng 114(2):146
Li X, Guan XP (2004) Time-frequency-analysis-based minor cutting edge fracture detection during end milling. Mech Syst Signal Process 18(6):1485–1496
Liu HQ, Chen QH, Li B, Mao XY, Mao KM, Peng FY (2011) On-line chatter detection using servo motor current signal in turning. Sci China Technol Sci 54(12):3119–3129
Kuljanic E, Sortino M, Totis G (2008) Multisensor approaches for chatter detection in milling. J Sound Vib 312(4–5):672–693
Tangjitsitcharoen S, Pongsathornwiwat N (2013) Development of chatter detection in milling processes. Int J Adv Manuf Technol 65(5–8):919–927
Song QH, Liu ZQ, Wan Y, Ju GG, Shi JH (2015) Application of Sherman-Morrison-Woodbury formulas in instantaneous dynamic of peripheral milling for thin-walled component. Int J Mech Sci 96-97:79–90
Liu C, Zhu L, Ni C (2017) The chatter identification in end milling based on combining EMD and WPD. Int J Adv Manuf Technol 91(9–12):1–10
Sheng Q, Zhao J, Wang T (2016) Three-dimensional stability prediction and chatter analysis in milling of thin-walled plate. Int J Adv Manuf Technol 86(5–8):2291–2300
Fang N, Pai PS, Edwards N (2014) A method of using Hoelder exponents to monitor tool-edge wear in high-speed finish machining. Int J Adv Manuf Technol 72(9–12):1593–1601
Mallat SG (2009) A wavelet tour of signal processing: the sparse. way 31(3):83–85
Yao Z, Mei D, Chen Z (2010) On-line chatter detection and identification based on wavelet and support vector machine. J Mater Process Technol 210(5):713–719
Cao HR, Lei YG, He ZG (2013) Chatter identification in end milling process using wavelet packets and Hilbert-Huang transform. Int J Mach Tools Manuf 69(3):11–19
Jiang AY, Zhang C (2006) Hybrid HMM/SVM method for predicting cutting chatter. Proc SPIE Int Soc Opt Eng 62801:8
Chen GS, Zheng QZ (2017) Online chatter detection of the end milling based on wavelet packet transform and support vector machine recursive feature elimination. Int J Adv Manuf Technol 5:1–10
Zhang Z, Li H, Meng G, Tu X, Cheng C (2016) Chatter detection in milling process based on the energy entropy of VMD and WPD. Int J Mach Tools Manuf 108:106–112
Sun Y, Zhuang C, Xiong Z (2014) Real-time chatter detection using the weighted wavelet packet entropy. Int Conf Adv Intel Mech 2014:1652–1657
Wang L, Liang M (2009) Chatter detection based on probability distribution of wavelet modulus maxima. Robot Comput Integr Manuf 25(6):989–998
Shi JH, Song QH, Liu ZQ, Ai X (2017) A novel stability prediction approach for thin-walled component milling considering material removing process. Chin J Aeronaut 30(5):1789–1798
Song QH, Shi JH, Liu ZQ, Wan Y (2016) A time-space discretization method in milling stability prediction of thin-walled component. Int J Adv Manuf Technol 2016:1–15
Cao H, Yue Y, Chen X, Zhang X (2016) Chatter detection in milling process based on synchrosqueezing transform of sound signals. Int J Adv Manuf Technol 2016:1–9
Lin J, Qu LS (2000) Feature extraction based on Morlet wavelet and its application for mechanical fault diagnosis. J Sound Vib 234(1):135–148
Yi H, Shu H (2012) The improvement of the Morlet wavelet for multi-period analysis of climate data. Compt Rendus Géosci 344(10):483–497
Ao Y, Qiao G (2010) Prognostics for drilling process with wavelet packet decomposition. Int J Adv Manuf Technol 50(1–4):47–52
Prakash M, Kanthababu M, Rajurkar KP (2015) Investigations on the effects of tool wear on chip formation mechanism and chip morphology using acoustic emission signal in the microendmilling of aluminum alloy. Int J Adv Manuf Technol 77(5–8):1499–1511
Seemuang N, Mcleay T, Slatter T (2016) Using spindle noise to monitor tool wear in a turning process. Int J Adv Manuf Technol 86(9–12):2781–2790
Acknowledgments
The authors are grateful to the financial supports of the National Natural Science Foundation of China (no. 51575319), Young Scholars Program of Shandong University (no. 2015WLJH31), the United Fund of Ministry of Education for Equipment Pre-research (no. 6141A02022116), and the Key Research and Development Plan of Shandong Province (no. 2018GGX103007).
Author information
Authors and Affiliations
Corresponding author
Ethics declarations
Conflict of interest
The authors declare that they have no conflict of interest.
Rights and permissions
About this article
Cite this article
Gao, J., Song, Q. & Liu, Z. Chatter detection and stability region acquisition in thin-walled workpiece milling based on CMWT. Int J Adv Manuf Technol 98, 699–713 (2018). https://doi.org/10.1007/s00170-018-2306-1
Received:
Accepted:
Published:
Issue Date:
DOI: https://doi.org/10.1007/s00170-018-2306-1